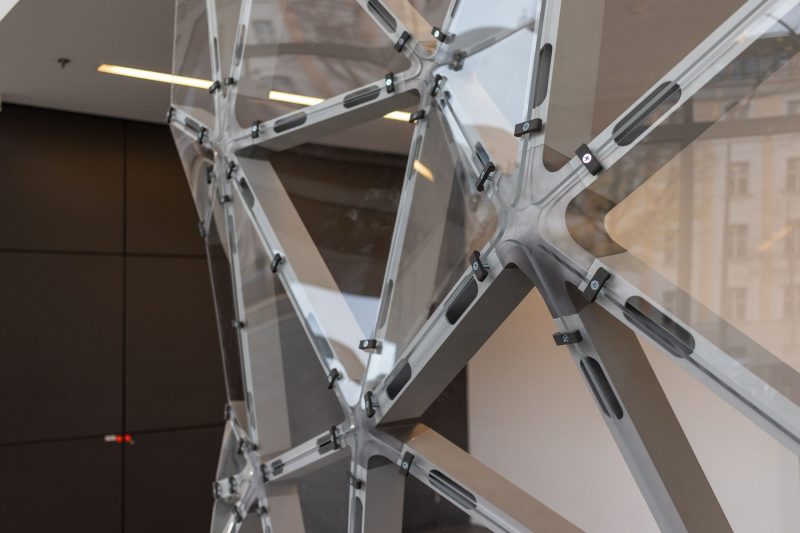
Nel settore delle costruzioni una delle vie di maggiore efficienza per quanto riguarda il risparmio dei costi della manodopera è sicuramente la standardizzazione. Dalla natura l’ispirazione per facciate standardizzate ad alta efficienza
Il gruppo di ricerca HTWK FLEX presso l’Università di scienze applicate di Lipsia ha progettato e prodotto con un processo completamente digitale il prototipo di una facciata in vetro (2×3 metri) che permette di realizzare in modo sostenibile non solo facciate ma anche coperture. Il modello di riferimento sono le strutture ad alte prestazioni a rete create in natura con un uso minimo di materiali.
Dall’unione di design e produzione il gruppo di ricerca FLEX ha utilizzato processi digitali e stampa 3D sviluppando un processo a catena completamente automatizzato e digitale in grado di realizzare nodi, ognuno con una propria geometria, collegati a elementi standardizzati per formare una struttura di supporto. Attraverso l’automazione e i processi di produzione generativa, è possibile risparmiare materiale, tempo e manodopera e, allo stesso tempo, realizzare geometrie individuali. I collegamenti delle aste, infatti, non devono essere realizzati a mano, ma stampati con precisione grazie al processo digitale Catene mentre le aste vengono saldate singolarmente ai nodi consentendo di risparmiare un’enorme quantità di lavoro.
Il processo InNoFa (Individual Node Facade) permette la realizzazione di una rete di aste standardizzate collegata a nodi in alluminio (in futuro anche in acciaio) stampati in 3D (44 aste per 12 connessioni) ognuno con una propria forma con garanzia di stabilità e minimo utilizzo di risorse attraverso la produzione automatizzata. Tale processo si basa sul concetto di costruzione ibrida ParaKnot3D, sviluppato da un’idea di Martin Dembski, che combina la tradizionale produzione in serie per strutture di superficie geometricamente semplici con elementi di nodo geometricamente complessi. L’utilizzo di questi nodi, che sono stati prodotti in modo additivo utilizzando il processo SLM (selective laser melting) presso l’Istituto Laser dell’Università di Scienze Applicate di Mittweida (LHM), è finalizzata alla realizzazione di una facciata polimorfa. Le connessioni utilizzano la generazione algoritmica della forma per ottenere transizioni a curvatura costante tra i profili cavi rettangolari.
Il gruppo di ricerca FLEX
Il gruppo di ricerca FLEX presso l’HTWK di Lipsia è un team interdisciplinare proveniente dai settori dell’architettura, dell’ingegneria civile e industriale. Sotto la direzione del Prof. Alexander Stahr, il gruppo di ricerca si dedica al collegamento digitale dei processi di pianificazione ed esecuzione, con l’obiettivo di utilizzare le risorse dell’architettura e della tecnologia di costruzione in modo più efficiente. Attraverso l’uso di strumenti digitali realizza costruzioni curve a basso consumo di materiale con geometria individuale.
foto D. Drucker ©Hochschule für Technik, Wirtschaft und Kultur Leipzig
a cura di Margherita Toffolon
Condividi l'articolo
Scegli su quale Social Network vuoi condividere